Большая Советская Энциклопедия (КО)
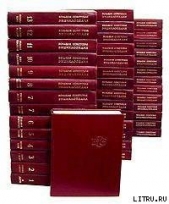
Большая Советская Энциклопедия (КО) читать книгу онлайн
Внимание! Книга может содержать контент только для совершеннолетних. Для несовершеннолетних чтение данного контента СТРОГО ЗАПРЕЩЕНО! Если в книге присутствует наличие пропаганды ЛГБТ и другого, запрещенного контента - просьба написать на почту [email protected] для удаления материала
Первая плавка чугуна целиком на коксе без добавки древесного угля впервые осуществлена в Великобритании в 1735. Коксовые печи с закрытыми камерами были впервые введены также в Великобритании в 30-х гг. 19 в. Длительное время производство кокса было придатком металлургической промышленности. Как самостоятельная отрасль К. п. возникла только в конце 19 в. В дореволюционной России производство кокса в промышленных масштабах началось в Донбассе в 80-х гг. 19 в. К. п. России была отсталой отраслью. В 1913 произведено менее 4,5 млн. т кокса. Около 20% внутренней потребности страны в коксе удовлетворялось импортом (около 1 млн. т в год). Коксовый газ использовался неэффективно, значительная его часть выпускалась в атмосферу. Химические производства на базе коксования углей находились на низком уровне. В период 1-й мировой войны 1914—18, Гражданской войны и военной интервенции 1918—20 производство кокса ещё больше сократилось. В СССР уровень 1913 достигнут в 1928—29. За годы Советской власти в разных районах страны сооружены крупные коксохимические заводы. Значительно расширилась сырьевая база. Освоен ряд новых угольных месторождений, в которых добываются угли для коксования — Кузнецкий, Карагандинский, Печорский угольные бассейны, Ткварчельское и Ткибульское угольные месторождения. Сооружения Магнитогорского, Кузнецкого, Нижнетагильского, Челябинского, Карагандинского, Орско-Халиловского и Руставского коксохимических заводов стало возможным только в связи с освоением новых баз углей для коксования (см. Коксующиеся угли ). Выпуск кокса в СССР непрерывно растет (см. табл.).
Производство кокса в СССР (млн. т валового кокса 6%-ной влажности)
1940 | 21,1 | 1970 | 75,4 |
1950 | 27,7 | 1971 | 78,3 |
1960 | 56,2 |
По производству кокса и по уровню развития К. п. СССР занимает (1971) 1-е место в мире.
Быстрое развитие коксования углей шло параллельно с ростом концентрации производства в К. п. В 1971 80% всего производства кокса осуществлялось на заводах с объёмом производства свыше 2 млн. т кокса в год. Это способствовало повышению технического уровня К. п. производство кокса в печах без улавливания химических продуктов прекращено. В СССР сооружаются современные коксовые печи, основные производственные процессы — разгрузка угля, загрузка и выгрузка коксовых печей, тушение кокса — полностью механизированы. По сравнению с дореволюционным временем период коксования углей и, следовательно, оборот коксовых печей ускорился в 2—2,5 раза. В К. п. внедрены непрерывные процессы при переработке химических продуктов коксования углей. Комбинирование коксохимических заводов с металлургическими и химическими заводами обеспечивает более рациональное использование коксового газа. Значительно увеличилась производительность труда в К. п. (за 1951—70 — в 2,2 раза). Росту производительности труда способствовало увеличение электровооружённости труда рабочих более чем в 3 раза. Основные направления дальнейшего развития К. п.: завершение комплексной механизации и автоматизации производственных процессов; интенсификация существующих и внедрение новых процессов коксования; расширение ассортимента углей, пригодных для коксования (использование газовых и слабоспекающихся углей); внедрение дистанционного и программного управления коксовыми машинами; осуществление мероприятий по улучшению условий труда и предотвращению загрязнения воздушного и водного бассейнов.
Успешно развивается К. п. и в др. социалистических странах, особенно в Польше и Чехословакии. В 1970 производство металлургического кокса в Польше составило 16,8 млн. т, в Чехословакии 11,5 млн. т.
В 1970 производство металлургического кокса в отдельных капиталистических странах составило (млн. т ): в США 57,7, ФРГ 39,9, Японии 25,1, Великобритании 16,5, Франции 14,2.
Лит.: Преображенский П. И., Обогащение углей для коксования, Хар. — М., 1950; Справочник коксохимика, т. 1—6 М., 1964-66; Улицкий Л. И., Экономика коксохимической промышленности СССР, М., 1964; его же, Экономика обогащения углей, М., 1969.
Л. И. Улицкий.
Коксохимия
Коксохи'мия, область химии и химической промышленности, занимающаяся переработкой природных топлив (главным образом каменного угля) в кокс и др. ценные продукты методом коксования . Основными коксохимическими продуктами (помимо кокса) являются коксовый газ , продукты переработки сырого бензола, каменноугольной смолы и аммиака (аммиачные удобрения); их полный ассортимент включает около 80 наименований (около 160 сортов). Ряд продуктов, подобных коксохимическим, получают также на нефтехимических предприятиях.
Коксование осуществляется в высокопроизводительных коксовых печах , обогреваемых низкокалорийным (доменным) или высококалорийным (коксовым и др.) газом. Сырьём для коксования служат специальные сорта каменных углей, способные спекаться (см. Коксующиеся угли ). Однако ввиду дефицитности таких углей перед коксованием обычно составляют смесь углей разных сортов (шихту). В шихту могут вводиться значительные количества самостоятельно не коксующихся углей, однако с таким расчетом, чтобы суммарные свойства шихты обеспечивали нормальный процесс коксования. Основным свойством, определяющим пригодность шихты для коксования, является ее способность образовывать при нагреве пластический слой достаточной толщины, вязкости и с требуемым ходом термического разложения. Проверка качества углей выполняется в лаборатории. Показателями служат толщина пластического слоя и усадка угля при коксовании. Последняя необходима для обеспечения выдачи «коксового пирога» из печи. Кроме того, состав шихты регламентируется по содержанию золы, серы, влаги и ряда других примесей. Для удаления из компонентов шихты нежелательных примесей угли предварительно обогащают и затем (для придания шихте однородности) тщательно смешивают, дробят (содержание фракции 3 мм в измельченной шихте должно быть около 95%).
Образующийся при коксовании сырой газ несёт с собой (в г/нм3 ): паров воды 250—450, паров смолы 100—120, бензольных углеводородов 30—40, аммиака — 8—13, сероводорода 5—30. Горячий (800 °С) газ охлаждают в газосборнике путём распыления в нём воды и затем в холодильниках (до 30—35 °С). Конденсат разделяют на аммиачную воду и каменноугольную смолу. Охлажденный газ засасывается мощными газодувками и нагнетается в систему улавливания и очистки. Здесь из газа улавливают пары сырого бензола, оставшуюся в газе большую часть аммиака, сероводород и цианистые соединения. Сырой бензол, каменноугольную смолу и аммиачную воду перерабатывают на товарные продукты.
В качестве примера ниже приведён материальный баланс коксования (в % ) одного из видов углей. Количество сухой угольной шихты (приход) 100,0.
Выход (расход)
кокс сухой................................................... | 78,0 |
смола............................................................ | 3,5 |
бензол......................................................... | 1,0 |
аммиак......................................................... | 0,3 |
коксовый газ сухой.................................... | 16,0 |
пирогенетическая влага.............................. | 1,2 |
Итого | 100,0 |
Очищенный коксовый газ, называется обратным; используется как топливо, а также в качестве сырья для синтеза аммиака.
Сопутствующий коксовому газу и являющийся вредной примесью сероводород превращают в элементарную серу или серную кислоту, цианистые соединения можно использовать для получения солей роданистоводородной кислоты и др. продуктов.