Беседы об АСУ
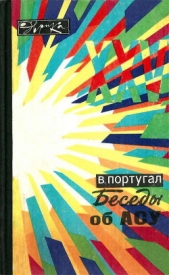
Беседы об АСУ читать книгу онлайн
Книга о создании и внедрении автоматизированных систем управления (АСУ), об идеях и принципах, заложенных в АСУ, о проблемах, возникающих при организации АСУ.
Внимание! Книга может содержать контент только для совершеннолетних. Для несовершеннолетних чтение данного контента СТРОГО ЗАПРЕЩЕНО! Если в книге присутствует наличие пропаганды ЛГБТ и другого, запрещенного контента - просьба написать на почту [email protected] для удаления материала

Следом за технологами нормировщики определяют трудоемкость каждого этапа. Трудоемкость измеряется в нормо-часах — в часах, которые надо затратить на изготовление изделия (машины). Например, трудоемкость работы в 10 тысяч нормо-часов означает, что данную работу один рабочий будет делать 10 тысяч часов, два рабочих — 5 тысяч часов, а сто рабочих — 100 часов.
Определив трудоемкость изготовления деталей для каждой машины, допустим, в 10 тысяч нормо-часов, нормировщики переходят к следующему важному моменту — расчету потребности в рабочей силе. Рассуждают они так. Общая трудоемкость работ по механическому цеху — 20 тысяч часов: один рабочий в год работает примерно по 2 тысячи часов, следовательно, для выполнения плана необходимо 10 рабочих (20 тыс. : 2). Аналогично по сборочному цеху необходимо также 10 рабочих.
Определив потребность в рабочей силе, сравнивают ее с численностью рабочих. Если в цехах действительно есть по 10 рабочих, прекрасно, рапортуется начальству, что план по труду сбалансирован (наличие равно потребности). Если рабочих больше, чем требуется, надо думать об увеличении плана, если меньше — либо уменьшать план, либо увеличивать число рабочих.
Но допустим, что в цехах все в порядке и по рабочим полный баланс. Производится последний расчет — определяется длительность выполнения каждой работы. Один из методов такой. Так как трудоемкость изготовления деталей для каждой машины по 10 тысяч часов, а работать будут 10 рабочих, следовательно, длительность работы — одна тысяча часов (10 тыс. : 10), или примерно полгода. На этом расчеты заканчиваются; составляется сводный план работ: срок выполнения каждой работы — полгода, срок выпуска обоих изделий — конец года; потребность в рабочей силе: 10 механиков, 10 сборщиков. Готовьте премию!
Такой метод расчета в настоящее время распространен на большинстве предприятий и называется балансовым (иногда объемным). Конечно, приведенный условный пример дает представление только о самом методе. Когда же такой расчет производится для большого предприятия, число изделий (номенклатура) которого достигает сотен наименований, а балансировать план нужно по сотням профессий, то весь плановый отдел в течение месяцев занят этим делом.
Но расчеты подходят к концу, наступает 1 января, и надо приступать к работе. И вот тут выясняется, что «гладко было на бумаге…».
В механическом цехе приступают к изготовлению «гаек и винтов» для изделия А и делают их, как положено, 6 месяцев. Попытка запустить в это же время «гайки и винты» для изделия Б оканчивается неудачей — ведь все 10 рабочих заняты на изготовлении изделия А. Приступить к изготовлению изделия Б они смогут лишь через полгода. К этому времени «гайки и винты» изделия А перейдут в сборочный цех.
Однако что же это? Конец года, а изготовлено только изделие А, а изделие Б еще надо полгода собирать! Аврал и штурм, всех переводят в сборщики, но план стараются выполнить! Попутно ищут виновных, чтобы наказать: почему с начала года не делали «гайки и винты» для изделия Б?
Виноват, несомненно, начальник механического цеха! Но он энергично возражает и доказывает, что если бы он выделил 5 рабочих на изделие А а 5 на изделие Б, то длительность цикла каждой работы была бы 12 месяцев (10 тыс. ч : 5 = 2 тыс. ч, или 1 год), то есть к концу года не собрали бы ни одного изделия. Так кто же виноват?
А никто. Виноват балансовый метод расчета, который не позволяет учесть, что перед тем, как детали поступят на сборку, их еще надо изготовить. Другими словами, балансовый метод не учитывает технологию изготовления изделий. Смотрите, как интересно получается: применили плохой метод для планирования, а это привело к штурмовщине и срыву планового задания, и в общем довольно трудно сразу разобраться, из-за чего все это произошло: то ли из-за того, что плохо работали, — то ли из-за плохого снабжения, то ли из-за чего еще… В процессе выполнения плана за год происходит столько всяких неурядиц — прогулы, аварии, задержки с поставками материалов, инструмента, — что очень легко переложить вину на них. А оказывается, план с самого начала был невыполним.
А зачем применять плохой метод планирования? Нет хороших? Есть. Еще в начале века один из последователей основоположника научной организации труда американца Ф. Тейлора, Г. Гант активно внедрял метод планирования с помощью диаграмм, учитывающих технологию изготовления изделия. Они, кстати, и называются гант-картами. Сейчас эта методика развита с помощью современного математического аппарата и названа календарным планированием.
Но вот в чем беда. Календарное планирование более трудоемко, чем объемное. Составить календарный план для предприятия с номенклатурой в сотни изделии, да еще при условии, когда изготовление каждого изделия состоит из нескольких сот этапов, практически для работников планового отдела невозможно. Ведь они еле справляются с объемными расчетами. И снова информационный барьер! Известен правильный метод, а пользоваться приходится неправильным потому, что только он доступен.
А вот с помощью ЭВМ можно планировать и календарными методами!
И так почти все и делают. Досконально изучив современные методы, выбирают наиболее подходящий для своих производственных условий, затем составляют программы расчета по этому методу на ЭВМ и планируют по-новому.
Но есть и исключения. Приходится сталкиваться со случаями, когда просто берут старые, балансовые методы и составляют программы расчета по ним. Вроде и планируют «по-новому» (ведь считает-то ЭВМ), а если глубже разобраться, то «эффект» почти тот же, что и в приведенном примере, — ведь методы-то планирования слишком грубы!
Почему же, имея под руками ЭВМ, не пользоваться более точными, пусть и более трудоемкими, методами? В основном эти случаи происходят из-за элементарной неграмотности, иногда из-за глупости с инициативой: учиться не хочется и, как у И. Ильфа и Е. Петрова, вместо автомобиля стряпают свою самоходную телегу, которая фордыбачит по буеракам.
Поэтому сейчас уже на институтской скамье учат: основной принцип создания АСУ — принцип новых задач. Он гласит, что при автоматизации не следует просто переводить на ЭВМ уже сложившиеся методы управления, а необходимо пересматривать эти методы в соответствии с теми огромными возможностями, которые представляет новая вычислительная техника.
В свете рассуждений об информационном барьере этот принцип означает следующее: когда автоматизируется та или иная функция управления, не следует стремиться только к высвобождению людей и к замене их труда машинным, как это происходит при автоматизации производства. Необходимо сначала проанализировать, какие беспорядки в управление внес информационный барьер, что уже потеряно и продолжает теряться. И, исходя из этого анализа, намечать новые задачи управления и новые методы решения. Правда, на самом деле чаще всего это старые задачи, которые за неимением достаточного количества людей не решались либо решались, но плохими, примитивными методами. А при автоматизации эти-то задачи никак не должны быть забыты.
Таков принцип новых задач или, если хотите, принцип старых задач! (Только не стоит рассматривать его как подтверждение житейского принципа, что все новое — это хорошо забытое старое.)
Итак, принцип новых задач — доминирующий принцип создания АСУ, действие которого распространяется еще на одну функцию управления — учет. И хотя он в меньшей степени подвергся разрушительному влиянию информационного барьера, чем другие функции управления, тем не менее и ему досталось. В частности, существенно уменьшилась частота учета и укрупнились единицы. Например, учет выполнения планов рабочими теперь уже проводится не ежедневно, а два раза в месяц: реже нельзя, ведь надо начислять зарплату. Выполнение плана цехом учитывается не по операциям, а по готовым деталям, иногда комплектам деталей. Текущая успеваемость студентов не учитывается — оцениваются только результаты сессии. И так везде. При внедрении АСУ, конечно, в первую очередь учет детализируется, становится более частым. И автоматизация его с объективно необходимыми частотой и подробностью приносит значительный эффект.