История электротехники
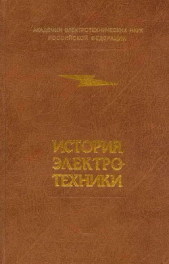
История электротехники читать книгу онлайн
Внимание! Книга может содержать контент только для совершеннолетних. Для несовершеннолетних чтение данного контента СТРОГО ЗАПРЕЩЕНО! Если в книге присутствует наличие пропаганды ЛГБТ и другого, запрещенного контента - просьба написать на почту [email protected] для удаления материала
Первые лазеры создали:
Т.Х. Майман (США, 1960 г.) — импульсный твердотельный лазер (на рубине);
А. Яван, В.Р Беннет, Д.Р. Херриот (США, 1961 г.) — непрерывно работающий гелиево-неоновый лазер;
Р.Н. Холл, М.Дж. Натан, Т.М. Квист (США, 1962 г.) — лазер на арсениде галлия;
С. Пател (США, 1964 г.) — лазер на углекислом газе.
В 90-х годах известны уже около 200 рабочих тел для получения лазерного излучения, однако для электротехнологии наиболее часто применяют лазеры на углекислом газе, позволяющие получить наибольшие значения мощности и КПД, и твердотельные (рубиновые), имеющие меньшие габариты и удобные в эксплуатации.
Плотность потока энергии в лазерном луче достигает весьма высоких значений (до 1∙1013 Вт/м2), чем главным образом и определяются технологические возможности лазерного нагрева.
Технологическое применение. Разработки лазерного оружия для «звездных войн» начались в США с начала 60-х годов, когда около 40 фирм получили правительственные заказы. С 1962 г. практически одновременно во всем мире началось технологическое применение лазеров: изготовление мельчайших отверстий, резка, сварка, поверхностная закалка. Фирма «Дженерал электрик» создала установку с использованием рубинового лазера для получения отверстий диаметром 0, 5 мм в алмазе за 0, 2 мс.
Первым процессом, внедренным в промышленность, являлось упрочение картера рулевого управления автомобиля в отделении фирмы «Дженерал моторе» (США) в 1974 г., при этом использовался лазер на углекислом газе мощностью 1 кВт.
В СССР первые лазерные технологические установки для поверхностной обработки были выпущены в 1964 г. на базе твердотельных лазеров типа «Квант» и газовых типа «Катунь», «Кардамон» и др. У первых установок с твердотельными лазерами для поверхностной обработки производительность и размеры обрабатываемого изделия были невелики. Переход на газовые лазеры позволил обеспечить значительно большую производительность.
В 1976 г. начались опытные работы по лазерному нагреву на ЗИЛе с участием МГУ им. М.В. Ломоносова и Института атомной энергии им. И.В. Курчатова (Е.П. Велихов). На предприятии запущена в производство автоматическая линия поверхностной лазерной обработки головок блоков цилиндров из алюминиевого сплава для двигателей внутреннего сгорания, внедрено упрочнение кромок вырубного пуансона, разработан процесс повышения износостойкости чугунного корпуса подшипника водяного насоса.
В 1978 г. началось промышленное применение лазерного нагрева на АЗЛК (г. Москва). Разработаны технология и оборудование с использованием газового лазера «Кардамон» для упрочнения коробки дифференциала заднего моста легкового автомобиля.
С 1964 г. лазерный луч нашел применение в биологии и медицине, например для приваривания сетчатой оболочки глаза.
С середины 70-х годов к работам по лазерному нагреву подключился ВНИИЭТО, где была создана лаборатория по использованию лазерного нагрева в промышленности.
7.2. ЭЛЕКТРИЧЕСКАЯ СВАРКА
7.2.1. ЭЛЕКТРИЧЕСКАЯ ДУГОВАЯ СВАРКА
Электрическая дуговая сварка была изобретена в России. Н.Н. Бенардос 6 июля 1885 г. подал заявку и получил привилегию Департамента торговли и мануфактур № 11982 (1886 г.) на способ «соединения и разъединения металлов непосредственным действием электрического тока» (рис. 7.11). Изобретение было запатентовано в Англии, Германии и некоторых других странах, причем эти патенты получены Н.Н. Бенардосом совместно с петербургским купцом С.А. Ольшевским, который финансировал зарубежное патентование.
Работы были начаты в 1881 г., а в 1885 г. в Петербурге на набережной р. Большой Невки, д. 41, была открыта показательная мастерская, в которой проводились сварочные работы по этому способу. Н.Н. Бенардос разрабатывал также автоматизацию сварки, применение инертных газов при сварке, сварку на переменном токе, подводную сварку и др. К середине 90-х годов XIX в. сварка по способу Н.Н. Бенардоса применялась более чем 100 заводами Западной Европы.

Н.Г. Славянов (1888 г.) предложил дуговую сварку с использованием расплавляемого электрода (рис. 7. 12). Этот метод впервые был использован в 1888 г. на Пермских казенных заводах при сварке вала паровой машины. В 1889 г. дуговая сварка по методу Славянова была использована на Пермских казенных заводах при строительстве парохода «Редедя князь Коссогский». В 1891 г. Н.Г. Славянов получил в Департаменте торговли и мануфактур привилегии № 8747 и 8748 на изобретения «электрической отливки металлов» и «электрического упрочнения металлов», а затем и патенты США и других стран. Им разрабатывались методы автоматического регулирования длины дуги, применения сварки под шлаком (использовалось дробленое стекло), использования предварительного подогрева свариваемых деталей, применения присадок ферросплавов для регулирования химического состава ванны и сварного шва.

В 1905 г. В.Ф. Миткевич предложил использовать трехфазную дугу для сварки металлов.
Одна из проблем электрической сварки — защита расплавленного металла от окисления и повышение устойчивости горения дуги, особенно при использовании плавящегося электрода. О. Кьельберг (Швеция, 1907 г.) предложил специальные покрытия для сварочных электродов, И. Ленгмюр (США, 1911 г.) разработал процесс дуговой сварки в атмосфере водорода, а позднее и с использованием других газов.
Параллельно с электрической сваркой развивалась и газовая сварка. Уже в 1902 г. А. Ле Шателье (Франция) применял кислородно-ацетиленовую сварку при ремонте паровых котлов. В 1903 г. Э. Фуше (Франция) получил патент на газовую сварочную горелку. Этот способ вскоре получил широкое распространение, что затормозило развитие электрической сварки. С 1908 г. на заводах Форда (США) стали применять газовую сварку. Во всем мире, в том числе и в России, газовая сварка стала применяться в различных отраслях промышленности.
Однако в 20-е годы развитие электрической сварки вновь продолжилось.
В 1919 г. фирма «Дженерал электрик» изготовила первую автоматическую дуговую сварочную головку. Подача электродной проволоки осуществлялась электродвигателем постоянного тока, а ток к электроду подводился через ролик. Длина дуги контролировалась по напряжению. В СССР автоматическую подачу электрода разработал в 1924 г. Д.А. Дульчевский. Он же применял угольный порошок при сварке меди для защиты от окисления.
Завод «Электрик» (г. Ленинград) внес значительный вклад в развитие электросварки в нашей стране: под руководством В.П. Никитина в 1924 г. были созданы первая электросварочная машина постоянного тока типа СМ-1 и сварочный трансформатор со встроенным регулятором (тип СТН). В 1926 г. начался выпуск машин для контактной сварки. В 1932–1933 гг. началось производство оборудования для автоматической дуговой и аргоноводородной сварки, был осуществлен выпуск первой в мире сварочной автоматической установки на переменном токе. В 1934 г. выпущен передвижной электросварочный агрегат типа САК-2, состоящий из бензинового двигателя Горьковского автозавода и сварочного генератора, смонтированных на общей раме. В 1947 г. начался серийный выпуск универсальных сварочных автоматов тракторного типа АДС-1000–1.
Первые применения сварки:
— в 1929 г. Николаевский судостроительный завод применяет дуговую сварку днищевых балок танкеров, а позднее и судовых трубопроводов; с 1931 г. в г. Магнитогорске при строительстве домны началось использование электрической сварки вместо клепки; (разрешение на сварку дал И.П. Бардин вопреки мнению американских специалистов, консультировавших строительство); при строительстве завода «Уралмаш» с помощью электрической сварки изготовили подкрановые балки пролетом 10 м; в том же 1931 г. началось внедрение дуговой сварки в мостостроение (Г.А. Николаев); на Западной железной дороге было установлено первое сварное пролетное строение длиной 19,8, а несколько позднее, в 1934 г.; на заводе «Стальмост» в г. Днепропетровске — цельносварное пролетное строение длиной 45 м; в те же годы изготовлены сварной мост (42 м) через водопад Челоне в США и однопролетный сварной мост решетчато-ферменного типа длиной 49,2 и шириной 8,25 м в г. Пльзень (Чехословакия).