История электротехники
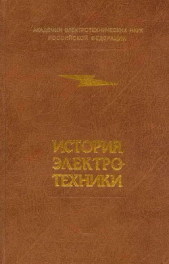
История электротехники читать книгу онлайн
Внимание! Книга может содержать контент только для совершеннолетних. Для несовершеннолетних чтение данного контента СТРОГО ЗАПРЕЩЕНО! Если в книге присутствует наличие пропаганды ЛГБТ и другого, запрещенного контента - просьба написать на почту [email protected] для удаления материала
В настоящее время практически все высоковольтные электрические машины выпускаются с термореактивной изоляцией, что обеспечивает высокий уровень надежности обмоток.
В заключение необходимо рассмотреть вопросы изоляции низковольтных электрических машин. До 1965 г. на заводе «Электросила» для низковольтных электрических машин переменного тока напряжением до 1200 В применялись две системы изоляции: 1) микалентная битумно-масляная для рабочих температур до 130 °С; 2) стекломикалентная на основе кремнийорганических связующих для рабочих температур до 180 °С. Последняя была создана на основе работ К.А. Андрианова по химии кремнийорганических материалов. Начиная с 1965 г., под руководством Е.П. Богдановой была разработана система изоляции на основе слюдопластовой бумаги производства Ленинградской слюдяной фабрики и эпоксидно-фенольных связующих класса нагревостойкости F.
С 1969 г. проводились разработки и внедрение полиимидной пленки и композиций на ее основе. Переход на пленочные материалы позволил снизить толщину изоляции примерно на 40%, соответственно повысились технические параметры электрической машины (коэффициент заполнения паза, удельная мощность). По техническим заданиям специалистов завода «Электросила» сотрудниками Всесоюзного научно-исследовательского института кабельной промышленности (ВНИИКП, г. Москва) был разработан провод с полиимидно-фторопластовой изоляцией с двусторонней толщиной 0,16 мм (выпускает завод «Москабель»). Уже в сериях машин постоянного тока П и 2П якорная обмотка выполнялась с использованием пленочных материалов.
Создание современной низковольтной изоляции проходило под руководством и при непосредственном участии Ю.Л. Преснова, В.В. Петрова и И.Т. Сушковой.
6.2.14. МЕТАЛЛОВЕДЕНИЕ ВТ КРУПНОМ ЭЛЕКТРОМАШИНОСТРОЕНИИ
Наряду с изоляцией очень важными элементами электрических машин являются металлы и сплавы. Основные исследования и разработки в области металловедения для крупного электромашиностроения проводятся в отделе металлов завода «Электросила». Главным исполнителем этих работ является Н.А. Греков. В результате творческого труда инженеров-металлургов как электротехнической, так и металлургической промышленности удалось создать стальные заготовки крупных размеров, набор специальных электротехнических и конструкционных металлов и сплавов, многие марки чистой электротехнической проводниковой меди и ее сплавов, разработать новые технологические процессы и способы контроля.
Производство заготовок роторных валов, несомненно, является важнейшей задачей при создании турбогенераторов. Ротор турбогенератора — это, пожалуй, самая крупная во всем машиностроении цельная металлическая деталь. Его масса изменяется от нескольких тонн (1,5–6) для небольших турбогенераторов мощностью 2–12 МВт до 200 т в чистой заготовке для тихоходного (1500 об/мин) турбогенератора мощностью 1000 МВт для атомных электростанций. Проблема изготовления роторов в нашей стране была удачно разрешена в самом начале производства генераторов, так как металлургическое производство других отраслей имело опыт изготовления требуемых слитков высококачественных сталей и их ковки в крупные заготовки, какими являются роторные валы.
Первые отечественные роторные заготовки создавались при совместном участии специалистов завода «Электросила» и завода «Баррикады» в г. Сталинграде (ныне Волгограде) еще в 30-е годы. По качеству они не уступали лучшим зарубежным аналогам фирм «Крупп», «Шкода», «Метрополитен-Викерс». В середине 70 -х годов в связи с необходимостью создания еще больших роторных заготовок, что было сопряжено с разработкой производства крупных стальных слитков (массой свыше 250 т), их производство параллельно с заводом «Баррикады» было налажено на Ижорском заводе (г. Ленинград), который постепенно стал специализироваться именно на производстве роторных заготовок особо крупных размеров для турбогенераторов мощностью 800, 1000 и 1200 МВт, а также для тихоходных турбогенераторов АЭС.
Наша страна вошла в число трех стран, выпускающих крупные заготовки роторов турбогенераторов (СССР, Япония, США). Этому способствовала деятельность специалистов-металлургов электротехнической промышленности И.А. Одинга, П.Р. Веррилепа, В.К. Дебрера, A.M. Шкатовой. И.А. Одинг был одним из первых исследователей во вновь организованной в 1922 г. лаборатории металлов завода «Электросила». Став членом-корреспондентом АН СССР, он непрерывно помогал лаборатории. П.Р. Веррилеп работал долгие годы главным металлургом завода «Электросила» (до 1964 г.). Он участвовал в организации производства роторов на заводе «Баррикады», за совершенствование технологии производства роторных заготовок был удостоен Государственной премии СССР Всю жизнь проработал на «Электросиле». В.К. Дебрер — неутомимый экспериментатор и изобретатель приборов и методик усталостной прочности роторных сталей. A.M. Шкатова — бессменный руководитель производства практически всех роторных заготовок как на заводе «Баррикады», так и на Ижорском заводе.
Немагнитные бандажные кольца — очень специфическая деталь турбогенератора. Внешняя простота их конфигурации и сравнительно небольшие массы (0,8–2,6 т) могут ввести в заблуждение относительно легкости изготовления этой детали. Можно сказать, что эта деталь является ключевой в конструкции ротора турбогенератора, а следовательно, и во всем генераторе. Полная немагнитность, высокие прочностные и пластические свойства (это самая нагруженная деталь во вращающемся роторе), наконец, надежная коррозионная стойкость — все эти требования сильно ограничивают выбор материала и усложняют технологию производства. Хорошей иллюстрацией сказанного является то, что во всем мире имеются лишь четыре завода, где могут быть надежно выполнены все требования заказчиков этого вида продукции. В первую очередь следует назвать фирму VSG (ранее «Крупп») в Эссене, которая удовлетворяет 2/3 потребности в бандажных кольцах всех мировых фирм, изготавливающих и ремонтирующих турбогенераторы. Три остальных завода (в Японии, Франции и России) в сумме производят 1/3 общей потребности. Заводы России способны в настоящее время изготовить современные, не уступающие по качеству и размеру зарубежным, бандажные кольца.
На заводе «Уралмаш» производят бандажные кольца из стали. Поскольку диаметр бандажных колец больше диаметра бочки ротора и они, кроме того, удерживают лобовые части обмотки ротора, то здесь требуется особенно высокая механическая прочность. Для этого используется холодное растяжение на гидравлическом прессе с усилием 30 тыс. т. В результате предел текучести может быть увеличен с 40 до 115 кг/мм (в зависимости от диаметра бандажного кольца). В последнее десятилетие удалось перейти на коррозионно-стойкие стали за счет введения в состав материала азота, увеличения содержания хрома и марганца. На заводе в г. Верхняя Салда освоено производство титановых бандажных колец. Следует отметить, что производство и применение бандажных колец из титановых сплавов до настоящего времени никем еще не повторено, несмотря на их бесспорные преимущества по совокупности технических и экономических характеристик. Следует заметить, что нагрев титановых колец перед посадкой на ротор должен быть больше, чем стальных бандажей, что исключает повреждение лобовых частей. В создание технологии изготовления бандажных колец существенный вклад внесли Г.И. Арковенко и Е.П. Силина.
Если в середине 60-х годов потребность в электротехнической стали в значительной мере удовлетворялась за счет импорта, то, начиная с 70-х и особенно в последние 15–20 лет, специализированные заводы нашей страны полностью удовлетворяют потребность отечественного электромашиностроения по номенклатуре и количеству электротехнической стали. Немало ценных исследовательских и опытных работ было проведено Верх-Исетским (г. Екатеринбург) и Липецким металлургическими заводами. Этому способствовали исключительная инициатива и творческое участие специалистов металлургов Т.А. Казариновой и В.Д. Дуриева.