История электротехники
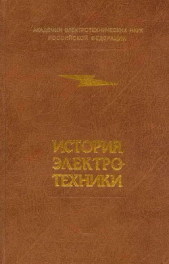
История электротехники читать книгу онлайн
Внимание! Книга может содержать контент только для совершеннолетних. Для несовершеннолетних чтение данного контента СТРОГО ЗАПРЕЩЕНО! Если в книге присутствует наличие пропаганды ЛГБТ и другого, запрещенного контента - просьба написать на почту [email protected] для удаления материала
6.2.7. ГИДРОГЕНЕРАТОРЫ
Создателем первого трехфазного синхронного гидрогенератора мощностью 220 кВт и частотой вращения 150 об/мин в 1891 г. был М.О. Доливо-Добровольский. Генератор был изготовлен в Швейцарии и установлен на ГЭС в Лауфене; он имел горизонтальный вал и был сочленен с вертикальной гидротурбиной конической зубчатой передачей. В 1900 г. фирма ASEA (Швеция) изготовила шесть гидрогенераторов вертикального исполнения мощностью 200 кВ∙А каждый для ГЭС в г. Вестерос. В 1907 г. эта же фирма поставила в Норвегию самый крупный в мире в то время гидрогенератор мощностью 10 500 кВ∙А.
В СССР первая крупная работа по гидрогенераторам связана с Волховской ГЭС. Четыре гидрогенератора для этой станции под руководством А.Е. Алексеева, Р.А. Лютера и А.С. Шварца по собственным чертежам изготовлял завод «Электросила», параллельно шведская фирма ASEA выполняла четыре аналогичные машины. Мощность каждого генератора равнялась 8750 кВ∙А, наружный диаметр 10 м, масса 250 т. Это были первые машины такого класса в Европе. Наши машины оказались лучше шведских по КПД, нагреву и массе.
Следующим этапом в развитии гидрогенераторостроения явился выпуск гидрогенераторов для Нижнесвирской и Верхнесвирской ГЭС.
Особое значение для производства гидрогенераторов имел уникальный заказ для Днепровской ГЭС: пять машин выполнялись американской фирмой «Дженерал электрик», а четыре — заводом «Электросила». Мощность каждой машины 62 МВт, масса 825 т. Изготовление генераторов было завершено в 1933 г. Под руководством технического директора завода А.Е. Алексеева был произведен разгон первого сварного ротора гидрогенератора до двойной частоты вращения в специально построенном на заводе разгонном устройстве с бетонной ямой. При восстановлении Днепрогэса после войны три генератора были заказаны фирме «Дженерал электрик», а шесть — заводу «Электросила». Использование лучших материалов и технических решений позволило увеличить мощность генератора до 72 МВт.
В послевоенные годы интенсивное строительство ГЭС проводилось в европейской части страны. Особое значение для страны имел каскад Волжских ГЭС. Разработка гидрогенераторов на заводе «Электросила» велась под руководством А.С. Еремеева. В связи с интенсивным развитием гидроэнергетики началось производство машин на заводах «Уралэлектротяжмаш» (г. Свердловск, ныне Екатеринбург), «Сибэлектротяжмаш» (г. Новосибирск) и «Электротяжмаш» (г. Харьков). Здесь необходимо отметить большой творческий вклад главных конструкторов гидрогенераторов указанных заводов: К.Ф. Костина, В.П. Лошкарева («Уралэлектротяжмаш»), B.C. Кильдишева («Электротяжмаш»), А.С. Постникова и Е.Е. Фишкина («Сибэлектротяжмаш»).
Как известно, мощные гидрогенераторы имеют низкие номинальные частоты вращения, и поэтому они превосходят все другие машины по габаритам, массам вращающихся частей и вращающим моментам. Элементы и узлы машин выполняются на заводе, а сборка — на электростанции. Генераторы обычно имеют вертикальное исполнение. В зависимости от расположения подпятника они могут быть зонтичного и подвесного типов. Использование гидроресурсов сибирских рек привело к созданию наиболее мощных ГЭС в мире. К таким относятся Братская, Усть-Илимская, Красноярская и Саяно-Шушенская ГЭС, на которых работают гидрогенераторы мощностью соответственно 200, 500 и 640 МВт.
Обычно гидрогенераторы имеют воздушное охлаждение. Однако для машин большой мощности с целью уменьшения их размеров и масс применяется водяное охлаждение обмотки статора и форсированное воздушное охлаждение обмотки ротора. Впервые в мире (1965 г.) водяное охлаждение обмотки статора было применено на гидрогенераторах мощностью 500 МВт и частотой вращения 93,8 об/мин Красноярской ГЭС. В дальнейшем оно было использовано как в более мощных машинах (640 МВт, 142,8 об/мин, Саяно-Шушенская ГЭС), так и в менее мощных (300 МВт, 200 об/мин, Нурекская ГЭС).
Повышение плотности тока в обмотке статора в связи с водяным охлаждением приводит к необходимости увеличения плотности тока и в обмотке ротора. Для этого требуется интенсивное охлаждение последней, что достигается с помощью форсированного воздушного или водяного охлаждения. В системе форсированного воздушного охлаждения воздух омывает обе боковые поверхности и проходит поперек проводников обмотки. Для этого между сердечником и катушкой делается круговой зазор, куда воздух идет из обода. Из этого зазора воздух поступает через поперечные каналы в межполюсное пространство. Это дает возможность теплового расширения сердечника в процессе эксплуатации. Более совершенный сердечник и новое крепление лобовых частей позволили добиться уникального результата: максимальная вибрация (двойная амплитуда) лобовых частей при номинальном токе статора составила 40 мкм.
Экспериментальные исследования гидрогенераторов Саяно-Шушенской ГЭС, проведенные Г.В. Карповым, показали, что максимальная длительная мощность генератора равна не расчетной 711 MB∙А, а 820 MB∙А. Следует заметить, что крупнейшие в мире гидрогенераторы ГЭС Итайпу (Бразилия, Парагвай) имеют мощность 823,6 MB∙А. Эти машины созданы фирмами «Броун Бовери» и «Сименс». Таким образом, генераторы Саяно-Шушенской ГЭС относятся к самым мощным в мире гидрогенераторам (рис. 6.5).

Разработка и производство гидрогенераторов для сибирских рек потребовали очень больших творческих усилий специалистов объединения «Электросила», работавших под руководством главного конструктора Н.П. Иванова, главного инженера П.М. Ипатова, конструкторов А.А. Дукштау и Ю.А. Дегусарова, а также руководителя расчетов Г.Б. Пинского.
Для применения более интенсивного охлаждения ротора ПО «Уралэлектротяжмаш» на Нурекской ГЭС последний, девятый генератор сделан с полностью водяным охлаждением. Здесь решающее значение имели совместные разработки машин главного конструктора В.П. Лошкарева, главных инженеров А.И. Казанцева и Ю.П. Глазкова.
В гидрогенераторах большой мощности (500 МВт и более) возникают очень большие электромагнитные силы. При обычных способах крепления частей появляются недопустимо высокие вибрации и повреждения обмоток. Такая аварийная ситуация произошла в 1969 г. на Красноярской ГЭС, когда от нагрузок до 300 МВт перешли к нагрузкам 400–500 МВт. Тогда еще не были ясны причины этой ситуации. На электростанции были собраны крупнейшие специалисты страны под руководством министра электротехнической промышленности А.К. Антонова. Причины аварий были найдены и определены пути их устранения. Они заключались в разработке новой системы крепления лобовых частей, улучшении системы водяного охлаждения и отказе от однослойной обмотки. В объединении «Электросила» были проведены исследования генератора, который являлся фактически натуральной моделью. На этой основе удалось найти технические и технологические решения, реализация которых на заводе и ГЭС позволила поднять уровень надежности гидрогенераторов.
К числу новых решений для улучшения вибрационных характеристик относится сборка сердечника статора на месте установки. Обычная конструкция статора из секторов создавала определенные трудности, связанные с их стыками. Поэтому сборка в кольцо была использована на самых мощных машинах — генераторах Саяно-Шушенской ГЭС.
Подпятник в гидрогенераторе является наиболее ответственным узлом. На протяжении десятилетий совершенствовались теория и расчет подпятников. Тем не менее этот узел очень труден для наладки и эксплуатации. В нашей стране и за рубежом применяются сегменты подпятника, состоящие из стальной основы и баббитового покрытия. Казалось, трудно было предложить что-то новое, более совершенное в этой хорошо освоенной области. И все-таки это оказалось возможным.
Крупным достижением отечественного гидрогенераторостроения явилось применение сегментов подпятника, облицованных фторопластом вместо баббита, которые разработал и внедрил Ю.Н. Байбородов. Сегмент такого типа, получивший название эластичного металлопластмассового (ЭМП) сегмента, состоит из стального основания и антифрикционного элемента. Антифрикционный элемент, образованный из опрессованной бронзовой проволоки с нанесенным на нее покрытием из фторопласта Ф4 толщиной 1,5–2,5 мм, припаивается к стальному основанию оловянным припоем. ЭМП сегменты характеризуются высокими противозадирными свойствами, при этом обеспечивается пуск без подачи масла под давлением. Генератор с такими сегментами может работать при самых малых скоростях. Удельное давление в подпятнике по данным испытаний на Братской ГЭС может быть доведено до 10 МПа. В настоящее время все гидрогенераторы страны выпускаются с такими подпятниками.